
Lynsey Laycock, Technical Director in our Civil and Structural team makes the case for structural reuse to reduce carbon emissions.
I keep hearing the term ‘urban mining’ being used in the construction world, so I’ve done a little digging (mining – get it!) to see what it’s all about.
Urban mining, in a construction sense, is when components within an existing building at the end of its life are dismantled and reused in the same (or very similar) form for a new building.
This forms part of the circular economy principle avoiding the processing energy it requires to take the same components and recycle them. Whilst recycling does avoid landfill waste and keeps materials (components) within the ‘in-use’ life cycle it has a fairly significant penalty to pay in terms of the energy usage for the recycling process and, typically, a down-grade in material properties.
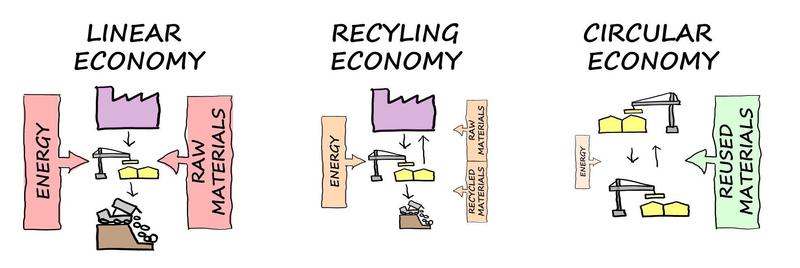
For structural engineers like myself, urban mining could look like a number of things but most likely we would be taking existing structural members, for example a steel beam, and reusing the same section as part of a new building frame.
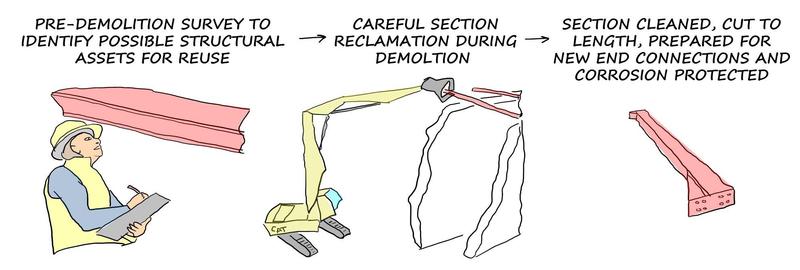
There are some serious carbon savings to be made by going through this process for reuse.
Here are two very telling facts for a steel section:
- Recycled steel = 1/2 ECO2e of virgin steel
- Reused steel = 1/8 ECO2e of virgin steel
Currently in the UK, it’s estimated that 99% of scrap structural sections are recovered, but only 6% are reused versus 93% that are recycled. So, there is definitely scope to improve this balance and save a lot of carbon emissions through urban mining.
It’s worth highlighting that the reuse of structural components is not limited to steel; concrete, timber and masonry have all been successfully ‘mined’ from existing buildings for use in new ones.
BedZED project shines a light on the opportunity
There are many successful projects that have used reused building components. For example, the BedZED project, a pioneering zero-carbon community project in the London Borough of Sutton, has utilised reclaimed structural steel sections from demolition sites in close proximity to the site - 98 tonnes in total equating to 95% of the project need.
They achieved this because the structural engineers provided specifications for a range of steel sections that could be used for each building element. This allowed steel to be sourced and purchased with more flexibility than a traditional engineering design where a single section size is specified.
What’s holding us back?
So why don’t we reuse structural elements in their current form more often?
Well, there are a number of barriers we need to overcome in order to successfully achieve this.
Barrier 1: Lack of information
Whilst we now benefit from BIM holding endless gigabytes of data with all the design information for buildings, this generally does not apply to the current building stock coming to the end of its life.
So, the first step in the urban mining process is to inspect the structure of a building, identify components that may be suitable for reuse, dismantle them, and then, if necessary, specify a series of tests to verify the material properties to allow us to carry out our structural design calculations for a new frame and justify the section for use. It can then be de-fabricated and stored ready for re-fabrication and use again.
Clearly there is a cost, time and risk balance within this process that needs to be weighed against the value of the components being ‘mined’ from the demolition.
Barrier 2: Timing
When one building is demolished it is not necessarily going to have the right components for reuse for another building due to be built in the near future.
Ideally, regional information on demolition and construction projects should be made easily available to allow supply and demand channels to be opened up.
Barrier 3: Regulations, policies and legislation
There are many national, regional and local initiatives in place to encourage sustainable construction, but currently there is not enough emphasis made on the potential carbon emission saving difference between recycling and reuse of materials.
For example, Landfill Tax has been successful in reducing the quantity of materials sent to landfill but doesn’t encourage reuse over recycling.
Barrier 4: Insurance
Professional indemnity insurance needs to allow for designers to specify reused materials.
It’s important that designers disclose any non-standard practices and get early engagement with their broker.
Insurers of buildings will also need to be engaged. It’s likely that insurance can be secured as long as prior agreement has been obtained and appropriate assessments / certifications are in place. This may require an independent on-site inspection.
Barrier 5: Current business models
It seems logical that reusing a structural section should be cheaper than buying new. However current business models are not set up in such a way to benefit from any cost savings, and so any incentive is lost and we revert to conventional procurement routes. We need to challenge our accepted thinking.
How to make reuse more common
So, if we’ve overcome the barriers, and we have a client, design team and contractor all fired up to reuse structural elements for a project, what do you do next?
Traditionally, a design team designs the structure up to detailed design stage and then suitable materials and components are purchased for construction.

The key to successfully reusing structural sections is to source the components of the building before the design has reached the detailed design stage.
This can become even more complex when the design of one element directly affects the specification of the next element; for example: beam spans may dictate the column grid and therefore column and foundation sizes, so an iterative design process is required.
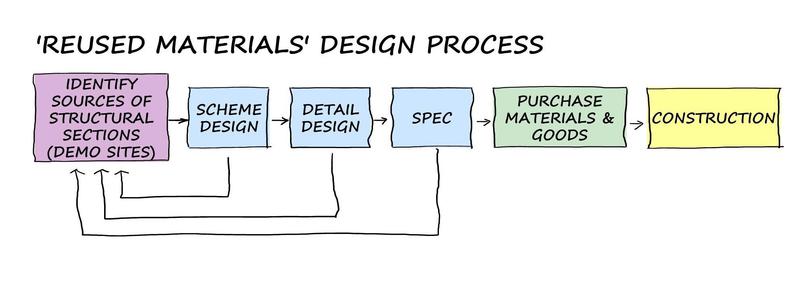
As a consequence, it may be necessary to bring forward the purchase stage within this process to ensure the availability of the reclaimed sections for construction.
For this to happen, the team needs to be able to identify buildings that are to be demolished and then identify potential sources of components from them. This means there is a significant benefit from using main contractors that carry out both demolition and construction works.
Longer term, the richness of data we hold from BIM and the emerging ‘digital golden thread’ will significantly aid our ability to identify building components that are ripe for reuse. It’s also a strong signal that we need to ensure that buildings are designed and built with deconstruction in mind to make them easier to dismantle to facilitate the reuse of components.
Learning from venue design
Dismantling and reuse is a process very familiar to the design and use of sporting arenas, stages, venues and other temporary structures. They are purposefully designed to be constructed in one location then dismantled and reconstructed somewhere else.
Simple lessons from this can be extended to structures with a longer life span, notably:
- Design simple, reversible connections between components
- Aim for single, non-composite elements
- Eliminate secondary finishes to materials
- Data is king, ensure information is recorded
It’s very clear that a significant reduction in emissions can be achieved through urban mining by reusing structural sections in their existing form.
We face challenges, but there are steps we should be taking now in terms of new build design to ensure that structures built today can be more easily broken back down into components for reuse when the building is demolished in the future.
This article was written by Lynsey Laycock, Technical Director in our Civil and Structural business.